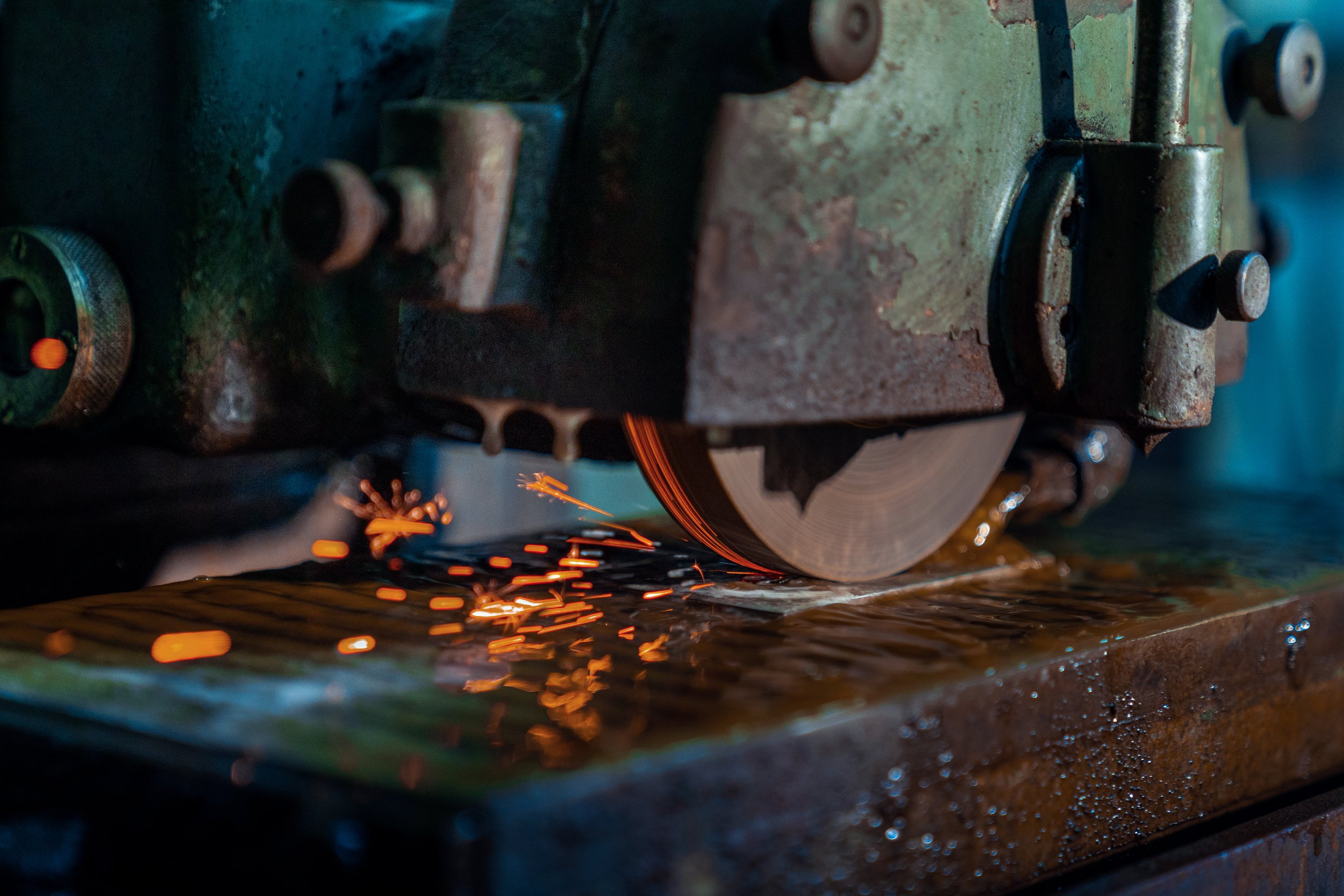
Shop Tour
“What tools do you need to make a knife?”
Its likely that you’ve seen knives being made. Knife making is depicted in movies, at renaissance fairs, and in popular television shows such as forged in fire. While the way knives are made in those depictions make for good entertainment, the reality is you might get bored watching my knives being made. Then again, you are here, so you must be interested.
What knife making looks like depends largely on whether the process is forging or stock removal. Forging involves heating up steel and plastically deforming it, usually via hammer and anvil. This is the more “exciting” kind of knife making, i.e. the stuff you see on television. Stock removal is a very different process. Like Michelangelo chipping away at everything that didn’t look like the statue of David, knife makers using the stock removal method will start with a piece of steel and grind away everything that doesn’t look like a finished knife. The process is usually much more tedious, and much less exciting. Stock removal and forging both finish the knife blade on a belt grinder. The tools used to make a knife will depend on the desired features, finish, the materials used, and ultimately the quality sought. A railroad spike can be hammered into shape with a sufficiently hot fire and a primitive hammer; the knives you will see here are more refined, and therefore require much more technologically advanced tools.
Here is a short list of the tools and equipment my shop has to offer, with descriptions of their use.
Shaping machines
2x72 Belt grinder. This style of grinder uses abrasive belts to grind away steel. Equipped with variable speed and spray coolant. Most of the magic of stock removal happens here.
EM Heald horizontal mill. This mill is used for slotting guards. Its a one trick pony but it does the job well.
Heat Treating
Evenheat 22.5KO knife kiln. This state of the art kiln allows me to heat treat a wide variety of steels, even difficult to heat treat steels, very precisely.
This is a Wilson hardness tester from an aerospace heat treatment facility. It precisely measures the hardness of steel, allowing me to verify my heat treatment process was done correctly.
Enco vertical mill. This mill allows me to machine features into steel very precisely, as well as create geometry that would not be possible simply be forging.
Hercules surface grinder. This surface grinder precisely flattens steel stock down to a desired thickness. It was made in northern Spain, likely in the 50s or 60s. The background at the top of the page is the same machine, up close.
Liquid nitrogen dewar. This holds liquid nitrogen and allows me to add cryogenic treatment to the heat treatment process. Cryogenic treatment at − 320 °F reduces the amount of retained austenite and gets the best performance from steel.